A new dimension of materials using selected density control of chemically crosslinking components by physical expansion.
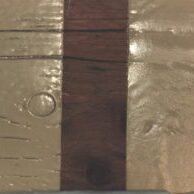
Left side - 20 mils of 100% solids polyurethane applied over cracked wood. Right side - 20 mils of the same material expanded three times using the ECOSYSTEM® expansion process.
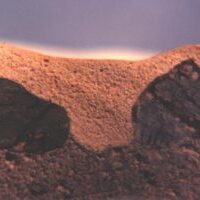
Cross-section view of the ECOSYSTEM® expansion process application of solvent-less polyurethane applied over severely degraded concrete.
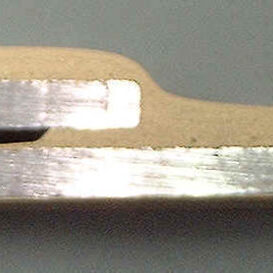
Cross-section view of the ECOSYSTEM® expansion process application of solvent-less polyurethane applied over skip welded steel plates.
The ECOSYSTEM® expansion process adds new dimensions for coatings through versatile and cost effective use of readily available liquid, chemically cross-linking 100 percent solids materials.
The ECOSYSTEM® process allows for new opportunities through the injection of an inert gas into the stream of the cross-linking materials prior to exiting the equipment (spray gun/pour nozzle) with selected density control. This process creates materials that can be deposited into a mold or onto a surface in a non-stressed, expanded closed cell, light weight, seamless monolithic condition. This process does not change chemical resistance or permeability characteristics as defined in the non-expanded solid condition.
The cellular nature of the expanded materials greatly enhances thermal properties when compared to the same material applied as a solid. This allows for the development of improved insulation materials without sacrificing chemical resistance.
While the ECOSYSTEM® expanded materials have the characteristics of foamed products, their flow and spray capabilities remain very similar to standard liquid coatings. This creates new alternatives for chemical containment by allowing for ECOSYSTEM® process applications of solvent-less materials direct-to-earth or on other extremely irregular surfaces as completely seamless non-stressed lining.
Due to lighter weight and lower density, the ECOSYSTEM® applied products offer high build and hang characteristics unmatched by traditional solid film materials while allowing for reduced raw material costs, elimination of CFC blowing agents, and the integration of filler products into the applied materials.
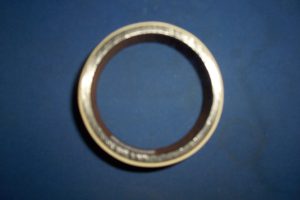
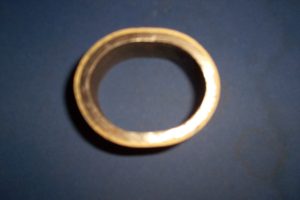
The above images of a pipe ring, have been coated with the RBU polyurethane and impacted, until out of round, with a hammer. You can see that the coating has not split.